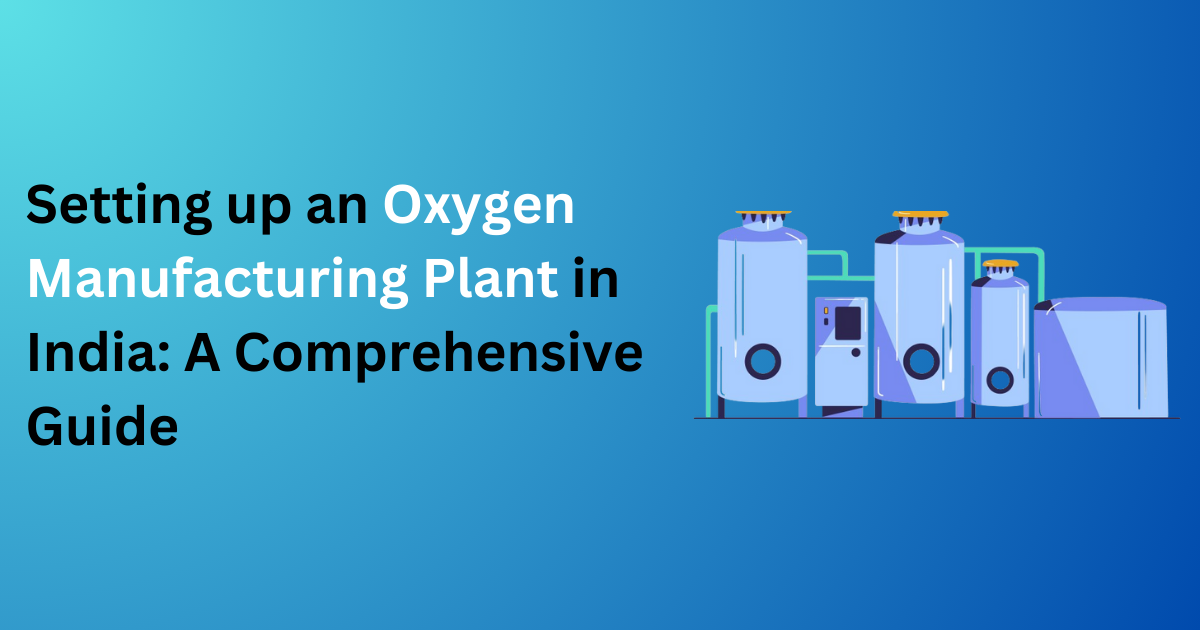
Setting Up An Oxygen Manufacturing Plant in India: A Comprehensive Guide
Introduction
In the intricate tapestry of healthcare, oxygen emerges as a fundamental thread, woven into the fabric of life-saving interventions. The global spotlight on healthcare infrastructure, accentuated by unprecedented challenges, has underscored the paramount importance of reliable and efficient sources of medical oxygen. As the demand for oxygen escalates, especially in regions like India, the need for self-sufficiency in production becomes evident.
Understanding the Market Landscape
Before embarking on the journey of setting up an oxygen manufacturing plant in India, a deep understanding of the market landscape is essential. The dynamics of the medical oxygen market are multifaceted, shaped by factors such as healthcare demands, regulatory frameworks, and the ever-evolving global health scenario.
Current Market Scenario:
-
Demand-Supply Dynamics: Analyzing the current demand for medical oxygen vis-à-vis the existing supply is paramount. A comprehensive assessment reveals gaps and opportunities, guiding strategic decisions in plant capacity and production planning.
-
Emerging Trends: Identifying emerging trends in medical oxygen usage, such as the rise in demand during healthcare crises, helps in anticipating future market needs.
Regulatory Considerations:
-
Licensing and Compliance: Navigating the regulatory landscape is critical. Understanding the licensing requirements and compliance standards set by regulatory authorities, particularly the Central Drugs Standard Control Organization (CDSCO) in India, lays the groundwork for legal and ethical operation.
-
Quality Standards: The market demands adherence to stringent quality standards. Familiarizing oneself with the Good Manufacturing Practices (GMP) and other quality benchmarks ensures the production of oxygen that meets medical-grade specifications.
Competitive Analysis:
-
Existing Players: Identifying and studying existing players in the medical oxygen market provides insights into competitive strategies, pricing models, and operational efficiencies.
-
Market Share and Positioning: Understanding the market share and positioning of established manufacturers aids in devising strategies for market entry and differentiation.
Regional Considerations:
-
Demand Variations: Recognizing regional variations in demand for medical oxygen is crucial. Different healthcare infrastructures, population densities, and healthcare facility distributions contribute to varied demand patterns.
-
Logistical Factors: Evaluating logistical factors, including transportation networks and proximity to healthcare facilities, guides decisions on plant location for optimal supply chain efficiency.
Global Health Scenario:
-
Pandemic Preparedness: Recent global health crises have highlighted the indispensable role of oxygen in healthcare. Assessing the impact of such events on the market and preparing for future health emergencies is a prudent consideration.
-
International Collaboration: Understanding global trends and potential collaborations with international entities can bring in diverse perspectives and foster innovation.
Preliminary Planning and Feasibility Assessment
Setting up an oxygen manufacturing plant requires meticulous planning and a comprehensive feasibility assessment. This phase serves as the foundation for informed decision-making, ensuring that the venture aligns with market needs, regulatory requirements, and long-term sustainability.
Assessing Regional Oxygen Demand:
-
Conducting Market Surveys: Engage in detailed market surveys to assess the specific oxygen demand in the targeted region. Understand the needs of healthcare facilities, industrial applications, and potential future requirements.
-
Collaboration with Healthcare Stakeholders: Consult with healthcare professionals, hospitals, and clinics to gauge their current and anticipated oxygen needs. Establishing partnerships early on fosters a collaborative approach.
Feasibility Study:
-
Financial Projections: Develop robust financial projections, considering initial setup costs, operational expenses, and revenue generation. This includes estimating production costs, pricing models, and potential returns on investment.
-
Risk Analysis: Conduct a comprehensive risk analysis to identify potential challenges and uncertainties. Assessing risks related to market fluctuations, regulatory changes, and operational issues aids in developing risk mitigation strategies.
Location Analysis:
-
Proximity to Demand Centers: Evaluate potential locations for the manufacturing plant based on their proximity to major demand centres. Minimizing transportation costs and optimizing supply chain efficiency are critical factors.
-
Infrastructure Availability: Assess the availability of essential infrastructure such as water, electricity, and transportation facilities. Proximity to reliable utilities contributes to operational stability.
Regulatory Landscape:
-
Understanding Licensing Requirements: Delve into the regulatory landscape, understanding the specific licensing requirements for oxygen manufacturing. Liaise with regulatory authorities, such as the CDSCO, to gain clarity on the necessary approvals.
-
Compliance Framework: Develop a thorough understanding of the compliance framework, ensuring that the plant design and operations align with regulatory standards. This includes adherence to GMP and other quality assurance measures.
Technology Selection:
-
Exploring Oxygen Production Technologies: Evaluate different technologies for oxygen production, considering factors such as efficiency, scalability, and environmental impact. Choosing the right technology is pivotal for long-term operational success.
-
Equipment Procurement Planning: Develop a plan for procuring the necessary equipment, ensuring that it meets industry standards and can accommodate future expansion.
Regulatory Compliance and Licensing
Understanding Regulatory Framework:
-
CDSCO Guidelines: Familiarize yourself with the specific guidelines and regulations provided by the CDSCO for the establishment and operation of oxygen manufacturing plants. This includes the Drugs and Cosmetics Act and Rules, as well as any specific guidelines related to medical gases.
-
Good Manufacturing Practices (GMP): Adherence to GMP is essential. Understand the GMP requirements outlined by the CDSCO for the manufacturing of medical gases, including oxygen.
Licensing Requirements:
-
Licensing Process: Initiate the licensing process by submitting the required applications to the CDSCO. This typically involves obtaining licenses such as a manufacturing license and a wholesale license for medical gases.
-
Site Master File (SMF): Prepare a comprehensive Site Master File detailing the facility’s layout, manufacturing processes, quality control measures, and other relevant information. This document is a crucial part of the licensing process.
Quality Control and Assurance:
-
Quality Control Measures: Implement robust quality control measures in line with CDSCO requirements. This includes regular testing of the oxygen produced to ensure it meets pharmacopoeial standards.
-
Quality Assurance Systems: Establish quality assurance systems to monitor and maintain the quality of the manufacturing processes. This involves documentation of procedures, validations, and adherence to quality management principles.
Personnel Training and Qualifications:
-
Personnel Training Programs: Develop training programs for personnel involved in the manufacturing process. Ensure that employees are adequately trained in GMP, safety protocols, and other relevant aspects.
-
Qualifications and Records: Maintain records of the qualifications and training of personnel. This documentation is essential for demonstrating compliance with regulatory requirements.
Environmental Compliance:
-
Environmental Impact Assessment: Ensure compliance with environmental regulations by conducting an environmental impact assessment. This includes assessing the potential environmental impact of the manufacturing processes and implementing measures for mitigation.
-
Waste Management: Develop effective waste management systems in accordance with environmental regulations. Proper disposal of waste gases and other by-products is crucial for environmental compliance.
Regular Audits and Inspections:
-
Internal Audits: Conduct regular internal audits to assess and ensure compliance with regulatory standards. This proactive approach helps identify and address potential issues before regulatory inspections.
-
Regulatory Inspections: Prepare for and cooperate with regulatory inspections conducted by the CDSCO. Maintain documentation, records, and evidence of compliance to facilitate smooth inspections.
Post-Market Surveillance:
-
Adverse Event Reporting: Implement a robust pharmacovigilance system for monitoring and reporting adverse events related to medical gases. Comply with CDSCO requirements for adverse event reporting.
-
Batch Release Procedures: Establish clear procedures for batch release, ensuring that each batch of oxygen meets the specified quality standards before being released to the market.
Documentation and Record Keeping:
-
Document Management Systems: Implement effective document management systems to organize and maintain records related to manufacturing, quality control, personnel training, and regulatory compliance.
-
Record Keeping: Maintain detailed records of all processes, procedures, and activities related to oxygen manufacturing. These records serve as evidence of compliance during regulatory inspections.
Plant Design and Technology Selection
The design of an oxygen manufacturing plant and the selection of appropriate technology are pivotal aspects that directly impact efficiency, safety, and the overall success of the venture. From the layout of the facility to the choice of production technology, each decision plays a crucial role in ensuring the reliable and sustainable production of medical-grade oxygen.
Infrastructure and Facility Setup
The infrastructure and setup of an oxygen manufacturing facility are critical components that directly influence the efficiency, safety, and regulatory compliance of the plant. From establishing a well-designed production area to implementing safety measures, every aspect of infrastructure plays a key role in ensuring the reliable production of medical-grade oxygen.
Operational Guidelines and Best Practices
Once the infrastructure is in place, establishing robust operational guidelines and adhering to best practices are essential for the smooth and efficient functioning of an oxygen manufacturing plant. Operational excellence ensures consistent production of high-quality medical-grade oxygen while maintaining compliance with regulatory standards.
Standard Operating Procedures (SOPs):
-
Develop comprehensive SOPs covering all aspects of oxygen production, from raw material handling to distribution. SOPs serve as a guide for employees and contribute to the consistency of operations.
-
Regularly review and update SOPs to incorporate improvements, changes in technology, and lessons learned from operational experiences.
Quality Control Protocols:
-
Implement stringent quality control protocols to monitor and verify the quality of oxygen at various stages of production. This includes routine testing for purity, moisture content, and other relevant parameters.
-
Establish sampling points and testing schedules to ensure that each batch of oxygen meets pharmacopoeial standards before release.
Equipment Calibration and Maintenance:
-
Develop a regular calibration and maintenance schedule for all equipment involved in the production process. This includes oxygen generators, compressors, and testing instruments.
-
Adhere to preventive maintenance practices to minimize downtime and ensure the reliability of equipment.
Personnel Training Programs:
-
Conduct regular training programs for plant operators and staff. Training should cover safety protocols, emergency response procedures, and updates on regulatory compliance.
-
Document and maintain records of personnel training, ensuring that all employees are well-versed in operational and safety requirements.
Process Optimization:
-
Continuously evaluate and optimize production processes to enhance efficiency. Implement process improvement initiatives based on data analysis and feedback from operational experiences.
-
Explore technological advancements in oxygen production and consider their integration to optimize processes.
Supply Chain Management
Efficient supply chain management is crucial for the success of an oxygen manufacturing plant, ensuring a seamless flow of raw materials, production processes, and timely distribution of medical-grade oxygen to end-users. A well-organized supply chain enhances reliability, reduces costs, and contributes to meeting the critical healthcare needs of the community.
Raw Material Procurement:
-
Develop strong relationships with reliable suppliers of raw materials, such as compressed air or oxygen-enriched air. Ensure a stable and quality supply chain for consistent production.
-
Implement just-in-time inventory practices to minimize excess inventory and associated holding costs.
Supplier Relationship Management:
-
Establish effective supplier relationship management practices. Regularly communicate with suppliers, share production forecasts, and collaborate to address any potential challenges.
-
Conduct periodic assessments of supplier performance, evaluating factors such as reliability, quality, and responsiveness.
Inventory Management:
-
Implement robust inventory management systems to track raw materials, work-in-progress, and finished goods. Strive for optimal inventory levels to meet demand without excess holding costs.
-
Utilize technology such as inventory tracking software to enhance accuracy and visibility in inventory management.
Production Planning and Scheduling:
-
Develop production plans based on demand forecasts, ensuring that production schedules align with market needs. Implement scheduling systems that optimize production efficiency and resource utilization.
-
Consider implementing advanced planning and scheduling (APS) tools for more accurate production planning.
Transportation and Logistics:
-
Optimize transportation routes for the distribution of medical-grade oxygen to healthcare facilities and industrial users. Minimize transportation costs while ensuring timely deliveries.
-
Collaborate with logistics partners to streamline the transportation process, considering factors such as route planning, vehicle capacity, and delivery timelines.
Environmental and Social Responsibility
In the context of an oxygen manufacturing plant, environmental and social responsibility is a fundamental aspect that goes beyond regulatory compliance. Demonstrating a commitment to sustainable practices and social well-being contributes to the overall positive impact of the plant on the community and the environment. Here are key considerations for environmental and social responsibility:
Financial Planning and Investment
Effective financial planning and strategic investment are integral components for the success and sustainability of an oxygen manufacturing plant. By aligning financial strategies with business goals, the plant can ensure optimal resource allocation, capitalize on growth opportunities, and navigate potential challenges. Here are key considerations for financial planning and investment:
Comprehensive Budgeting:
-
Develop comprehensive budgets that encompass all aspects of plant operations, including raw material procurement, production processes, distribution, and overhead costs.
-
Consider both short-term and long-term budgets to facilitate strategic financial planning.
Cost Analysis and Control:
-
Conduct thorough cost analyses to identify areas for cost reduction and operational efficiency improvements.
-
Implement cost control measures to manage expenses and optimize resource utilization.
Revenue Forecasting:
-
Develop realistic revenue forecasts based on market demand, pricing strategies, and production capacity.
-
Regularly review and adjust revenue forecasts in response to market dynamics and changes in demand.
Working Capital Management:
-
Implement effective working capital management practices to ensure sufficient liquidity for day-to-day operations.
-
Monitor and manage inventory levels, accounts receivable, and accounts payable to optimize cash flow.
Investment in Technology:
-
Allocate funds for technological investments that enhance operational efficiency and competitiveness. This may include automation, process optimization technologies, and data analytics.
-
Evaluate the return on investment (ROI) for technology initiatives to ensure they align with business objectives.
Conclusion
Setting up an oxygen manufacturing plant in India is not just a business venture; it’s a commitment to the nation’s healthcare infrastructure. By following this comprehensive guide, individuals and organizations can navigate the complexities, contribute to healthcare resilience, and ensure the availability of life-saving oxygen to those in need. This initiative not only addresses the current demand but also positions stakeholders as key contributors to the future of healthcare delivery in India.